Purchasing pre-owned machinery for food processing can be a strategic move for businesses looking to expand or upgrade their production capabilities without incurring the high costs of new equipment. Key factors such as the equipment’s condition, compliance with food safety standards, and the availability of parts must be carefully evaluated. Finding a reliable source for used food processing equipment can significantly impact your operational efficiency and bottom line. Keep reading to discover the essential considerations that will guide you in making a well-informed investment in used food processing machinery.
Assessing the Condition and Quality of Used Food Processing Equipment
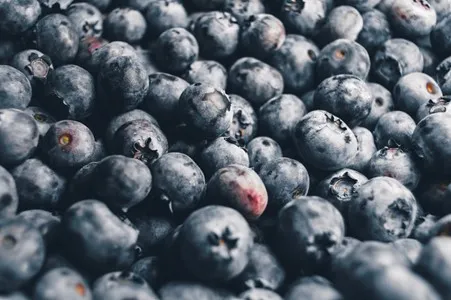
When considering pre-owned food processing equipment, the foremost concern is its current condition. Well-maintained machinery can offer long-term service, but a thorough inspection is essential to detect wear, corrosion, or damage, including critical components like motors, blades, and electronics.
Reputable sellers should provide transparent history, including usage, maintenance records, and repairs. Understanding its operational background can predict future performance and maintenance needs. Look for warranties or guarantees for added assurance.
Consider hiring a professional technician for a comprehensive assessment to identify hidden issues and ensure the equipment meets production requirements. Factor in potential repair costs and request operational manuals for future maintenance.
Compatibility and Integration with Existing Production Lines
When implementing new manufacturing equipment or technologies, compatibility and integration with existing production lines are vital. Professionals must evaluate factors like size, power requirements, communication protocols, and programming interfaces to ensure seamless operations.
The goal is to integrate new machinery without disrupting productivity, often requiring modifications or customization. Prioritizing compatibility minimizes downtime, reduces rework, and optimizes production output. It also facilitates easier maintenance and future upgrades, leading to streamlined workflows and a competitive edge in the industry.
Understanding the Aftermarket Support and Spare Parts Availability
When investing in used machinery, ensuring uninterrupted operation is crucial. The availability of spare parts for your specific model and brand should be thoroughly investigated to avoid obsolescence due to component failure.
Reliable aftermarket support, including technical assistance, customer service, and access to service technicians, is essential. Inadequate support can lead to increased downtime and maintenance costs.
Consider the cost and lead times for obtaining spare parts. Delays in procurement can disrupt production cycles, so prioritizing equipment with accessible components is wise. Some businesses preemptively purchase critical spare parts to minimize potential disruptions.
Building partnerships with reliable suppliers who offer ongoing support and parts is key to equipment longevity. Establishing these relationships and understanding the support system is crucial before finalizing any machinery purchase.
Ensuring Compliance with Food Safety Regulations and Standards
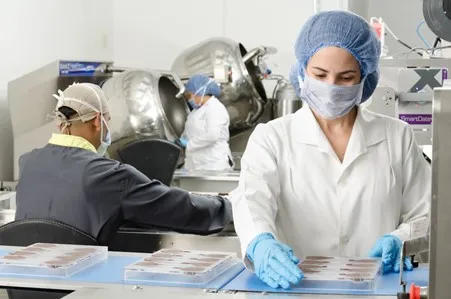
Ensuring compliance with food safety regulations is paramount in the food processing industry. When purchasing used machinery, it’s crucial to verify that it meets current standards to protect consumers and prevent legal issues.
Inspect materials and surfaces for compliance with food safety standards, prioritizing food-grade stainless steel and easily cleanable materials to minimize contamination risks. Verify that the equipment’s design allows for thorough cleaning and sanitization.
Traceability is vital for swift response in case of quality control issues or recalls. Make sure the machinery can integrate into traceability systems to track product batches effectively.
Seek guidance from legal experts or consultants specializing in food industry regulations to ensure all compliance requirements are met. They can assist with certification and documentation processes for used equipment.
Evaluating the Return on Investment of Pre-Owned Food Machinery
Assessing the financial viability of investing in used food processing equipment involves calculating the total cost of ownership. This encompasses purchase price, shipping, installation, maintenance, and potential upgrades. Comparing this with the cost of new equipment reveals potential savings.
Consider operational efficiencies the machinery offers, such as increased productivity, reduced labor costs, or expanded product lines, all of which contribute to ROI.
Factor in the resale value of well-maintained equipment from reputable brands, which often retains considerable value, allowing for potential recouping of the initial investment upon resale.
Seeking advice from financial advisors or utilizing cost analysis tools can provide an objective view of the long-term financial benefits. Conducting a thorough cost-benefit analysis ensures an informed decision that aligns with operational goals and budget.
Overall, when evaluating used food processing equipment, it’s essential to balance benefits with potential risks and costs. Assessing the equipment’s condition, integration capabilities, aftermarket support, adherence to food safety standards, and ROI is key to making a wise and profitable investment. By carefully considering these factors, businesses can leverage high-quality pre-owned machinery without sacrificing efficiency or safety.